Handlungsfeldanalyse II: Von der Idee zur Umsetzung
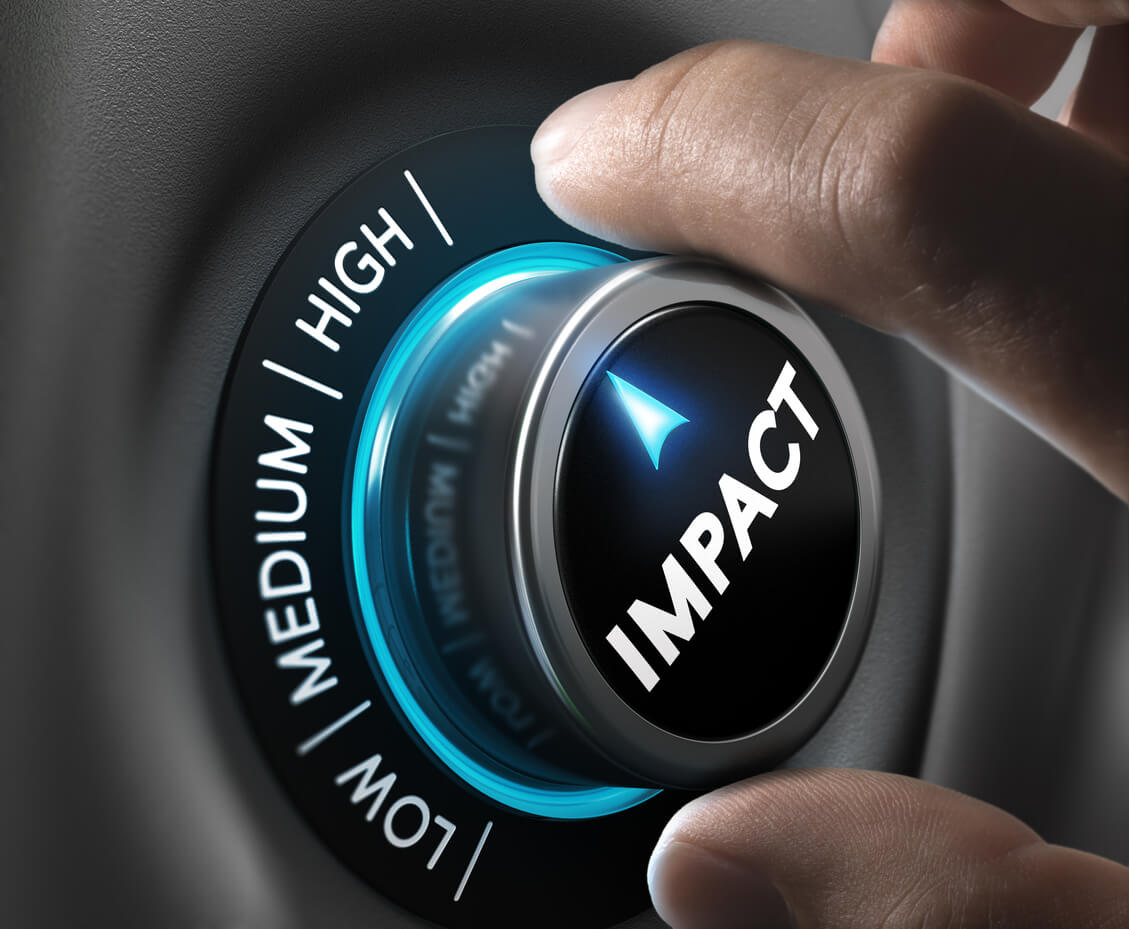
Fallbeispiel: Zusammenfassung und Beschreibung der Ausgangssituation
Vorangegangene Blogartikel machten bereits deutlich, dass sich unser Beratungsansatz der Philosophie des Network Thinkings verschrieben hat. Kurzum: Die kollaborative Verbindung von verschiedenen Disziplinen und (Fach) Expertenansichten schafft kreative und innovative Lösungsansätze.
Der Handlungsfeldanalyse nachgelagert folgt in gleicher Personenrunde ein Abschlussgespräch über die Resultate der Analyse sowie die Definition der im Detail zu analysierenden Handlungsfelder. Für ein praxisnahes Verständnis erinnern wir uns noch einmal auszugsweise an folgenden Inhalt aus dem letzten Artikel:
„Weiterhin wurde während der Diskussion herausgearbeitet, dass es teilweise Probleme mit den Stammdaten gibt, die sich offenbaren, wenn das System für Kommissionierlisten mit verschiedenen Artikeln die korrekte Standardverpackung für den Versand ermitteln soll.“
Kurze Randnotiz: Der Hinweis kam von einem Lagermitarbeiter und ist hierarchisch über den Lagerleiter an den verantwortlichen Ressortleiter getragen worden.
In Handlungsfelder aggregiert betrifft dieser Punkt die Felder „Lager“ und „Transport“. Logistiker wissen, dass diese beiden Themengebiete der Wissenschaftsdisziplin Logistik differenzierte Wissensanforderungen benötigen. Der Bereich „Transport“ befasst sich mit der außerbetrieblichen Logistik. Hierbei soll raum-zeitliche Gütertransformation durch eine möglichst effiziente Nutzung und Kombination der unterschiedlichen Verkehrsträger (Straße, Wasser, Luft) von der Quelle zur Senke stattfinden. Sprich: Ein möglichst günstiger Transport vom Produzenten zum Endkunden oder vom Lieferanten zum Produzenten.
Bei der innerbetrieblichen Logistik geht es um die logistischen Tätigkeiten innerhalb des eigenen Werkes. Themen wie Produktionsversorgung, Intralogistik, Lagerung und der Versand von Produkten. Während im Feld Transport meistens mit externen Spediteuren und Logistikdienstleistern zusammengearbeitet wird, wird im Feld Lager häufig auf eigenes Personal gesetzt. Zusätzlich impliziert das Stichwort „Stammdatenproblem“, dass auch die IT-Abteilung unter Umständen in diese Thematik inhaltlich involviert ist.
Fassen wir noch einmal kurz zusammen:
- Das System im Bereich Versand ermittelt nicht immer die korrekte Verpackungseinheit
- Prima vista sind falsche Stammdaten der Grund
- Zur Bearbeitung des Problems sind Fachleute aus den Abteilungen Lager, Transport und IT notwendig
In vier Schritten mit Design Thinking zur Lösung
Nach der Zusammenfassung stellt sich die Frage, wie wir mit den bisher gewonnen Erkenntnissen umgehen. Die Antwort lautet: Inkrementell in vier Phasen.
- Phase
Untersuche! Machen Sie sich ein Bild von den Auswirkungen. Recherchieren Sie den Kontext, Zusammenhänge und Abhängigkeiten. - Phase
Verstehe! Graben Sie tiefer und versuchen Sie das Thema aus der Nutzerperspektive zu verstehen. Beleuchten Sie Einflussfaktoren, Akteure, Prozesse und Beziehungen aus verschiedenen Perspektiven. - Phase
Ideen! Entwickeln Sie im Team gemeinsame Ideen und Sichtweisen, möglichst breit gefächert unter Berücksichtigung aller vertretenen Disziplinen. - Phase
Experimentiere! Schnelles Übertragen der Ideen in visuelle Darstellungen und wenn der Aufgabe dienlich einfache, angreifbare Prototypen.
In der ersten Phase wurde gemeinsam untersucht welche Auswirkungen durch die falsche Wahl der Versandeinheit entstehen. Dabei kam heraus, dass der Kunde im Versand elf verschiedene Standardverpackungen (Kartonagen) im Einsatz hat und das System durch die Artikel auf der Kommissionierliste dem Versandmitarbeiter automatisch vorgibt, welche Kartonage dieser für die Auslieferung zu wählen hat. Auffällig ist, dass 5 dieser 11 Kartonagen, also rund die Hälfte, bei KEP Dienstleistern als Übergröße deklariert werden. Das heißt, es fallen zusätzliche Handlingkosten pro Paket an, die zwischen 2,5 Euro und 5 Euro variieren können, abhängig vom Dienstleister. Eine andere mögliche Auswirkung ist, dass eine zu kleine Kartonage vorgegeben wird. In diesem Fall nimmt der Lagermitarbeiter die nächst größere Kartonage.
Die zweite Phase dient dazu die Auswirkungen in ein tieferes Verständnis zu überführen und die inhärenten Prozesse und Fehlerkosten zu verstehen. Eine Analyse der Versendungen ergab, dass täglich 400 Pakete aus dem Zentrallager verschickt werden und davon rund 30 % (= 120 Pakete) in den Kartonagen versendet werden, die durch die Dienstleister als „übergroß“ deklariert werden. Dabei werden ca. 90 % zu 5 Euro je Karton und 10 % zu 2,50 Euro je Karton versendet; die Kosten sind eine zusätzliche Rechnungsposition und fallen zzgl. zu den Frachtkosten an. In der Summe fallen pro Tag also rund 570 EUR für übergroße Paketsendungen an. Extrapoliert per anno sind es somit 135 bis 140 Tausend Euro.
Die weiteren Fragen lauten nun: Wie hoch ist der Anteil an Sendungen, die bei korrekter Berechnung der Verpackungseinheit mit einer Kartonage versendet werden können, die keine Übergröße haben und wie ermitteln wir diesen Anteil?
Die Fragen leiten die dritte Phase ein: Ideen! Es sollen gemeinsam Ideen und Ansätze gesammelt werden, die a) die Fehlerkosten messbar machen b) die Fehler kurzfristig beheben und c) dafür sorgen zukünftig solche Fehler zu vermeiden.
Bei einer geringen Anzahl von Artikeln, wäre es möglich die realen Maße der Artikel mit den Werten der Stammdaten abzugleichen. Bei einer Zahl von über 18.000 Artikeln ist dieser Ansatz jedoch nicht passend.
Eine andere Möglichkeit wäre durch den Einkauf noch einmal die aktuellen Abmessungen aller Artikel von den Lieferanten anzufordern und so die Stammdaten anzupassen. Dies ist analog zu erstem Ansatz auf Grund der notwendigen Ressourcen kein gangbarer Weg und führt leicht zu Unmut auf der Seite der Lieferanten, wenn unterstellt wird, dass die übergebenen Informationen eventuell Fehler enthalten.
Die gemeinsame Lösung umsetzen
Final wurde ein empirischer Ansatz in Kombination mit technischer Unterstützung gewählt, um die gestellten Fragen nachweislich zu beantworten. Die Lagermitarbeiter, welche die Kommissionierlisten bearbeiten und die Artikel im Karton verpacken, wurden alle gebrieft wie folgt zu verfahren: Immer, wenn der Lagermitarbeiter das Gefühl hat, dass die Artikel in eine kleinere Kartonage passen, soll er austesten, ob sich seine Ahnung bestätigt. Lässt sich der Auftrag in einer kleineren Kartonage verschicken, so wurde die Lieferscheinnummer angescannt und in einer separaten Applikation weggespeichert.
Das Ergebnis war eine Auftragsliste mit allen Artikelnummern, die eventuell mit falschen Maßen in den Stammdaten gepflegt sind und somit eine falsche Verpackungsauswahl zur Folge haben. Die Anzahl der Artikel wurde signifikant eingegrenzt. Weiterhin war man nun in der Lage den monetären Effekt zu bewerten, der durch die Stammdatenfehler entsteht. Einmal in der Woche wurde die Liste von Auszubildenden und Lagermitarbeitern abgearbeitet, d.h. die betroffenen Artikel wurden aus dem Regal geholt und neu vermessen. Bei Abweichungen zu den Stammdaten wurden die Abmessungen des Artikels im System angepasst. Über die Zeitachse ist die Liste deutlich kürzer geworden und nach einem Monat wurde eine erste Evaluierung der Fehlerkosten vorgenommen. Nach drei Monaten wurde das ganze wiederholt.
Die Ergebnisse in der Zusammenfassung:
- die falschen Abmessungen konnten auf eine geringe Anzahl von Lieferanten eingegrenzt und korrigiert werden
- Die Fehlerkosten durch die Auswahl falscher Kartonagen belief sich nach finaler Schätzung auf ca. 40 k€ per anno
- Das Unternehmen denkt über ein Kamerasystem nach, welches Abmessungen von (neuen) Artikeln automatisch vornehmen kann
- Abweichungen von den Stammdaten im ERP-System sollen dann automatisch angepasst und zusätzlich an den Lieferanten gemeldet werden
Das beschriebene Beispiel zeigt, wie durch die Kombination von verschiedenen Mitarbeitern und technischen Hilfsmitteln Fehlerkosten analysiert, reduziert und im späteren Prozess komplett vermieden werden können.
Laden Sie sich unser Design Thinking Template kostenlos herunter.
Neueste Kommentare